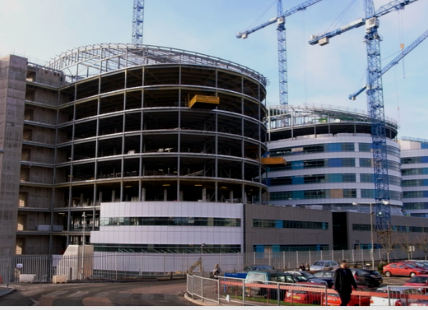
How to Manage Inbound Capital Equipment & Meet Your Building Load Schedule
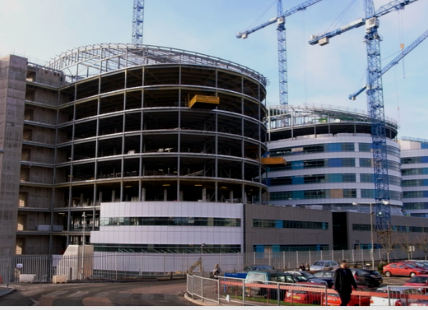
A large university health system in the mid-west was building a new children's hospital on their main campus. The 550,000 square foot facility is located next to the existing hospital which created an extremely congested area for equipment deliveries to the project site.
The university announced plans early on to commence the building load by floor following the completed construction of specific floors. This meant that construction traffic and new equipment deliveries would occur simultaneously. The university knew it needed a choreographed logistics solution to manage the inbound equipment and grant the contractors access to the docks to keep construction on track.
A Unique Transportation Management Solution
After a competitive bidding process, the university signed a contract with the Healthcare Group at Beltmann Integrated Logistics (BIL). Beltmann collaborated with the owner's capital management team, their transition consultant and the medical equipment planner to develop a logistics solution for the capital equipment aspect of the project.
The BIL team identified several key takeaways:
- Just in time deliveries to the site would not be feasible as freight carriers could not pinpoint an exact delivery time.
- Dock appointments needed to be scheduled in advance of deliveries and definitive delivery time windows and would be assigned to inbound carriers.
- Un-scheduled deliveries cold not be permitted as they caused disruptions to workflows at the project site.
With these tenants in mind, BIL drafted a logistics plan to control all inbound capital equipment transportation to off-site warehousing. The plan had two key attributes:
- Control inbound capital equipment traffic from the manufacturer to the warehouse. This process enabled BIL to determine the purchase order status before release from the manufacturer and ensure that automated purchasing systems did not route the freight to the main hospital receiving dock.
- Stage the equipment at the warehouse into specific floor quantities and load these shipments onto vehicles for an exact sequenced delivery schedule.
A Unique Transportation Management Solution
The daily procedure involved a finely tuned process of: obtaining floor releases from the contractor, coordinating dock appointments for multiple modalities with the transition planner, cross referencing pre-floor manifests provided by the equipment planner with on-hand warehouse inventories; and BIL on-site team managing an efficient pull of equipment using inventory tracking systems, staging and loading trucks for several project delivery stops and ensuring that every delivery requirement and timeframe was met.
Contingencies were met with alternative planning and scheduling, so the master activation schedule was kept on track despite various delays.
Win/Win
A post project analysis revealed that a win/win scenario had taken place. Not only did Beltmann meet the required building load schedule, our Transportation Management program gave the client two key tools for this project:
- Inbound transportation of capital equipment was controlled through one entity, Beltmann. This innovation enabled the client to change delivery schedules to minutely fit the changing requirements of the building load schedule.
- The BIL Transportation Management program generated savings on freight services of 20-30% over manufacturer based "pre-pay and add freight programs".
The Beltmann Transportation Management program gave the client:
- Firm management controls over the flow of equipment to the project site.
- Eliminated un-announced shipments of capital equipment to the main hospital receiving dock.
- Generated savings on freight of 20-30% on a fixed fee basis.
Contact Beltmann Integrated Logistics
To improve your transportation management process or inquire about your newest project, contact Beltmann Integrated Logistics today.
Healthcare Logistics 101 COVID-19 has had a significant impact on healthcare practices, staff and processes. If you don’t already outsource your healthcare logistics, now may be the time to act. This article will help you better understand what healthcare logistics includes and how it can help your business. How Can Healthcare Logistics Help My Team? Flexibility to Meet Your Neesd. One of the great things about working with 3PL is that you can plick and choose from the services you need. Your 3PL team should have the experiience and ability to provide all related services, and be able to increase and decrease the services they provide for you as and when required. Next time you need to send or received PPE urgently or need to open a temporary facility due to an influx of patientss, your 3PL will be by your side to help make this happen as efficiently as possible, and ahve the flexibility to meet your needs. Save Time & Money. Your team is doing essential work. Give your internal team members the time they need to focus on their areas of expertise. A professional 3PL will be able to use its expertise to get the job done quickly and streamline processes. Working with 3PL can also help you save money. 3PLs may also benefit from preferred pricing and know how and when to negotiate. Combined Healthcare & Logistics Expertise. Choose a 3PL team with specialist healthcare experience. It is essential that you feel you can trust your 3PL team to handle, deliver, move and install high value equipment and have an understanding of your industry. A 3PL will have logistics expertise that your internal team can’t match. If you choose a 3PL with healthcare logistics experience, they will be able to combine their healthcare industry insight with their knowledge of logistics to provide optimal support and help you move towards more efficient processes. Get Started Now. We specialize in healthcare equipment logistics and medical relocations. Contact us today to learn more about how we can help. Learn more at www.beltmannlogistics.com